Breakthrough in Ion Exchange Resin Technology: Zero Sludge Discharge Achieved in Thallium-Containing Wastewater Treatment at Chinese Lead Smelter
- Share
- Issue Time
- Mar 10,2025
Summary
On March 10, 2025, a Chinese lead smelter achieved zero sludge discharge in thallium-containing wastewater treatment through advanced ion exchange resin technology. By integrating oxidation-precipitation and resin adsorption, the process achieved 98% thallium recovery and eliminated sludge disposal costs, reducing chemical consumption by 30%. This innovation sets a benchmark for heavy metal pollution control and accelerates green smelting under China's dual carbon strategy.
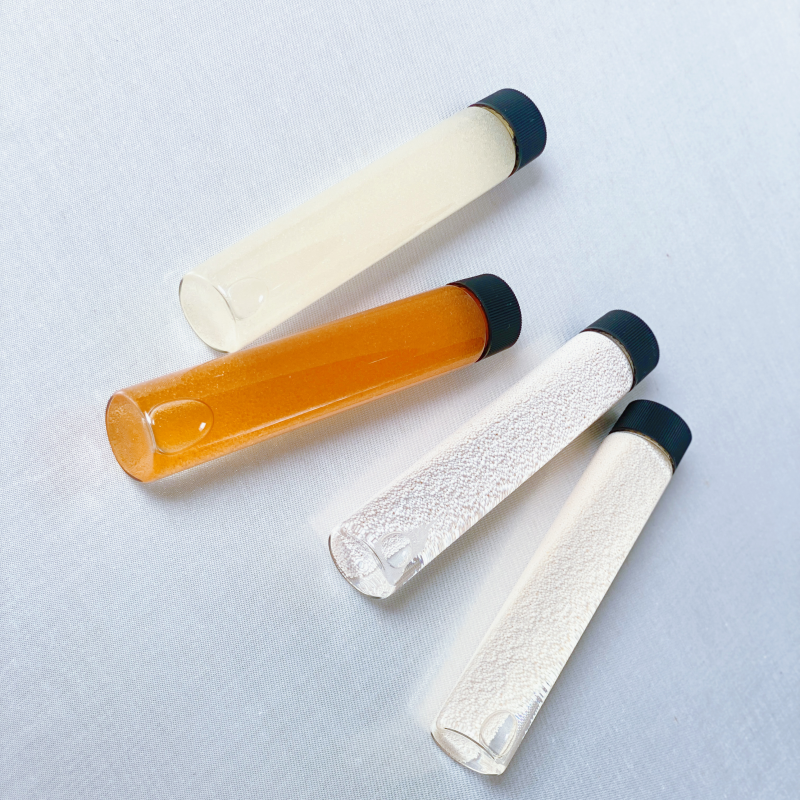
Breakthrough in Ion Exchange Resin Technology: Zero Sludge Discharge Achieved in Thallium-Containing Wastewater Treatment at Chinese Lead Smelter
1. Technological Breakthrough: From Hazardous Waste to Resource Efficiency
The lead smelter adopted RCX-5143 ion exchange resin developed by Kehaisi, optimizing traditional oxidation methods with the following steps :
Step 1: Potassium permanganate (KMnO₄) oxidizes Tl⁺ to Tl³⁺, forming stable TlCl₄⁻ complexes.
Step 2: Selective adsorption of thallium complexes by ion exchange resin, achieving a capacity of 1.2 g Tl/g resin.
Step 3: Resin regeneration using sodium sulfite (Na₂SO₃), recovering thallium concentrate (purity >99%) with a 95% reuse rate.
2. Activated Carbon Synergy: Dual Safeguards for Water Safety
To address complex pollutants, the plant deployed coconut shell activated carbon systems (iodine value ≥800), targeting organic sulfides and residual chloride ions. Key findings :
Collaborative Efficiency: Activated carbon-resin integration increased COD removal to 92%, outperforming standalone methods (activated carbon: 78%; resin: 85%).
Material Innovation: Spherical activated carbon derived from sulfonic acid-based cation exchange resin via CO₂ activation exhibits high mechanical strength (compressive resistance ≥50 MPa) and controlled pore distribution (microporosity >70%).