The influence of ash content on the structure and properties of activated carbon
- Share
- Issue Time
- Mar 11,2025
Summary
Ash significantly reduces the adsorption and electrochemical properties of activated carbon by consuming activators, blocking pores, and disrupting the double layer structure. Future research should further explore the interaction mechanism between ash content and carbon matrix, and develop efficient and environmentally friendly ash removal technologies to meet the refined requirements of activated carbon performance in different application scenarios.
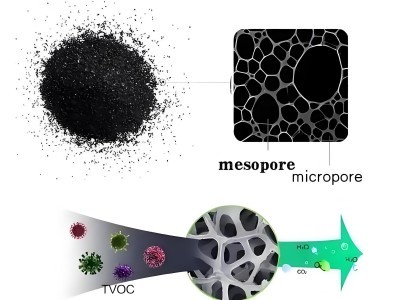
The influence of ash content on the preparation process of activated carbon
Ash undergoes side reactions with activators (such as KOH, water vapor, etc.) during the activation process, generating non-volatile salts (such as K ₂ SiO ∝, KAlO ₂), resulting in a decrease in effective activators. To achieve the predetermined activation effect, an additional amount of activator (about 5% -7%) and energy consumption (temperature increase of about 7%) are required. Experiments have shown that the activation efficiency of raw materials after ash removal is significantly improved. For example, the adsorption capacity of ash removal coal can be doubled under the conditions of reducing the amount of activator by 5% and reducing the temperature by 7%. This indicates that the presence of ash not only increases production costs, but also reduces carbon conversion efficiency.
The influence of ash content on the pore structure of activated carbon
Optimization strategy for ash removal process
The timing and method of ash removal should comprehensively consider the characteristics of raw materials and target applications:Pickling/alkaline washing options: Pickling with HCl, HF, etc. can effectively remove metal oxides, but it is highly corrosive to equipment; NaOH alkaline washing is suitable for removing silicates.Ash removal sequence: Some studies suggest removing ash before activation to reduce activator consumption, but the cost of pretreatment needs to be balanced.Process control: By optimizing the activation temperature, time, and type of activator, the negative impact of ash content can be partially offset.